Gunpowder, Auto Refinishing, and Jeff Gordon—Two Centuries of DuPont
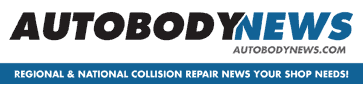
Thursday, 23 December 2010 20:08
Featured in AUTOBODYNEWS
What’s the connection between black gunpowder, auto refinishing, and Jeff Gordon? In a word: DuPont. On December 10, 2010, DuPont held a grand opening to dedicate their new Coatings Technology Center at the Experimental Station in Wilmington, Delaware, only a short distance from where DuPont’s legacy began with the manufacturing of gunpowder at Eleutherian Mills—now known as Hagley—in 1802. The opening celebration consisted of a tour of the new facility, and Hagley Museum and a memorable lunch with NASCAR-champ Jeff Gordon.
DuPont’s Experimental Station in Wilmington is the site of extensive research that has lead to many game-changing inventions, such as nylon, Kevlar and Teflon.
DuPont invited a small group of media representatives to tour the new facility and learn about the many steps involved in their coatings technology process. As a Wilmington resident with a long-term interest in DuPont’s presence in our community, I was more than happy to be invited.
After beginning the day with a complimentary breakfast at the DuPont Country Club, the tour group boarded a chartered bus which carried us the short distance to the Experimental Station where the dedication ceremony was to take place. While guests and DuPont employees huddled in a heated tent, DuPont executives talked about the importance of the new center and their goals as a company.
Robert Roop, the manager of the Coatings Technology Center, spoke of his excitement in having DuPont’s other industries in close proximity. The Chief Science and Technology Officer, Douglas Muzyka, said a goal of the new center was to bring customers and science together to improve modern automobile coatings.
According to Lewis Manring, Vice President of DuPont Performance Coatings (DPC), DuPont’s core value has been based on innovation for over two hundred years, and the invention of Duco paint in 1920 brought color to the automobile industry. (According to the company’s website, DuPont began producing nitrocellulose-based pyroxylin lacquers after acquiring the International Smokeless Powder & Solvents Company in 1905. The purchase of the Arlington Company ten years later deepened the company’s involvement. Although they were quick drying and widely used on brass fixtures, conventional lacquers were too brittle for more demanding uses. By the 1920s, however, the automotive industry had become a huge potential market. Although mass production had vastly increased output, because conventional paints took up to two weeks to dry, finishing remained a bottleneck. In 1920 DuPont’s chemists produced a thick pyroxylin lacquer which was quick drying but durable and that could be colored. DuPont marketed it under the name Viscolac® in 1921. Assisted by General Motors engineers, DuPont refined the product further and renamed it Duco®. The success of Duco led to further experimentation with finishes and, late in the 1920s, DuPont developed Dulux®, an even more effective alkyd finish.)
John McCool, President of DPC, assured customers that the Coatings Technology Center shares DuPont’s goals of innovation, differentiation and productivity, and by emphasizing efficiency and effectiveness, they will focus on “developing things our customers can use so they can be better in the future as well.”
After McCool cut the blue ribbon to dedicate the new Coatings Technology Center, we were lead into building 402, one of two buildings at the Experimental Station, for their tour of the facility. Upstairs our tour was divided into six groups, with DuPont employees joining the tours while employees at the Coatings Technology Center acted as tour guides.
Dom Barsotti and Violeta Petkovski began by discussing the analytical aspect of DuPont’s Coating Technology Center in a short presentation titled Measurement Science and Technology. Their goals are quality, regulatory support, stability and performance.
DuPont paints are comprised of twenty to thirty ingredients, and the analytical department ensures that the components are combined in the correct proportions. There are three layers: the first protecting from corrosion; the second providing color; the third acts as a protecting gloss. When a defect is found, such as roughness in the finished surface, analysts search for impurities. The methods range from spectroscopy to chromatography and microscopy, with other, more exotic techniques, available as well.
In discussing Undercoat Technology, Junping Li, Pat Horan and Scott Ryan listed their goals as environmental friendliness, productivity, and corrosion resistance. Undercoats consist of multiple layers of primers and sealers, and DuPont works to provide a highly protective coating system, utilizing anti-corrosive pigments. Waterborne paints such as Cromax-Pro® utilize wet-on-wet technology which minimizes flash time between coats as there is no longer a need to wait for the paint to dry before applying a subsequent coat. Additionally, this is a paint that will deliver performance in a single coat.
Balancing VOC, productivity and appearance are the goals of Clearcoat Technology, according to Joan Hansen and Irving Bell. The clearcoats from DuPont Performance Coatings consist of solvents, monomers and initiators. They also provide UV protection in their clear gloss to help maintain appearance of the paint. This department particular performs small scale adaptation of what would occur in a production facility, slowly increasing to a plant-size scale to reduce volatile content and enhance productivity. They focus on improving the cure rate which is the key to early buffing, as well as consistency which ensures that the customers will receive the same product time after time.
Tony Moy, a dispersion engineer, and Rick Wilson lead the discussion on Pigmented Dispersion. Their focus is on colored pigments, the dispersion process, and quality analysis. They begin by breaking the pigment down in a milling process, along with dispersant, grind resin and media. The media comes in various densities, sizes and appearances, all of which influence the correct color. Their main goal is stability which will ensure that the paint will settle rather than separate into layers on the shelves. Good dispersion must diffuse uniformly and will appear homogenous, but poor dispersion results in voids from pigment separation. Dispersion is required for solid colors, and the pigments, the color portion of the paint, determine whether the paint will be opaque or transparent.
The Colorcoat presentation, guided by Burt Palmer and Brian Priore, emphasized the importance of aesthetics, environmental stewardship and customer driven attributes. Naturally, the colorcoat is the visible layer. It is made from a mixture of pigment dispersion, polymers (large, film-forming resins) and liquid additives, which give viscosity to the paint.
Another focus of the Colorcoat department is meeting regulatory needs and helping their customer to do so, by removing some of the organic solvents from their mixture and lowered the intrinsic viscosity of polymers. They have also replaced 90–95 percent of the formerly organic solvents with water, often referred to as the “universal solvent.”
DuPont tries to assist customers by providing them with quality product that meets industry standards. To improve productivity, they’re working on reducing drying time, improving the cure rate and increasing hiding strength of their paints. Employing the principles of rheology, the science of flow, helps them understand the interactions between pigment dispersions, polymers and additives. Mechanically, they work to improve chip resistance, hardness, color durability and adhesion through the use of rigorous and controlled processes which develop and control the architecture of the polymers.
In their discussion on Color Science, Dan Benton and Judy Obetz list their department’s goals as providing state-of-the-art color technology, outstanding color matches, and color tools. The use of color proofing has improved customer productivity, and DuPont Performance Coatings now employs its Xpert Mixing System which allows them to select the color, adjust the color, and blend it to judge acceptability. They use lights and microscopes to verify accuracy and consistency of color, which improves productivity for customers by faster cycle times and increased profitability.
DuPont will release a new color deck during the second week of January, 2011, and new color technology is scheduled to debut in April 2011.
Crossing the parking lot, we were greeted by John Moore in the processing lab. He explained the goals of the application process are customer process simulation, product robustness testing and spray characterization. These scientists thoroughly test under what conditions the product works or does not work in order to guarantee product performance. By using vertical and horizontal spray robots, they are able to perform statistically designed experiments to predict performance and ensure product robustness while emitting near zero emissions. The labs are designed to allow testing in different environments since the products must work everywhere. Additionally, DuPont has a group who tests their products in the field in various geographies before a product is released, and they are always eager to receive feedback from customers.
In the Product Testing Area, Ross Morgan and Kurt Hankerson, along with their team, test products to ensure that they deliver what they are designed to do. In order to test durability, they use accelerated simulations, predictive performance and produce difference experiments.
Though products are tested by a panel at DuPont’s facility in Florida, due to the high sunlight and humidity, this group improves timelines by administering accelerated tests through the use of machine-generated sunlight, humidity and UVB light which tests the products’ reaction to exposure to these elements. To test the products, they cycle high-to-low temperatures on a sample to test its reaction to various environmental factors, and they test chip resistance by firing stones at painted panels. For any product that DuPont wants to introduce, the Product Testing Area experiments to ensure that the product meets manufacturer requirements; however, their tests can also be based upon customer requests.
Once the tour of the Coatings Technology Center was completed, we guests continued to Terrace on the Hill, DuPont’s restaurant at the Experimental Station, where we were treated to a buffet-style catered lunch. After sampling a special cake made to celebrate the dedication of the new facility, we were introduced to the promised special guest, NASCAR’s four-time Winston Cup Series champion, Jeff Gordon.
Gordon entered the restaurant to thunderous applause and cheerfully answered questions that were relayed to him by a DuPont employee, Harry Hall. He discussed his sponsorship and happiness with the results from the 2010 season and his goals for next season. He also mentioned his appreciation at spending the holiday season with his wife, Ingrid, and their two children, Ella and Leo. After all questions were answered, DuPont’s guests followed Gordon back to building 402 where we were given the opportunity to take photographs with the NASCAR legend and receive a personalized autograph. Jeff Gordon left a lasting impression and was a memorable highlight of Friday’s event.
Guests boarded the chartered bus once again and we were taken down the road to Hagley Museum where they received a tour of the gunpowder mill where DuPont’s legacy began. We saw exhibits on workers who operated the gunpowder mills during the late nineteenth century, the stone mills and waterwheels, and simple machine technology such as wheels, axles, levers, gears and pulleys.
One display focused on Eleutherian Mills as it was the first DuPont home in America, and this exhibit included domestic, farm and powder-yard vehicles from up to two hundred years ago. Another exhibit focused on the Explosives Era when Hagley manufactured black gunpowder. DuPont Science and Discovery demonstrates the company’s transition from a manufacturer of explosives in the nineteenth century to an ultra-modern research firm which does much more than coatings, one which has improved many aspects of everyday life. The museum efficiently concluded the grand opening and dedication of DuPont’s Performance Coatings’ new Coatings Technology Center by reminding customers of DuPont’s two-century legacy and continued success.